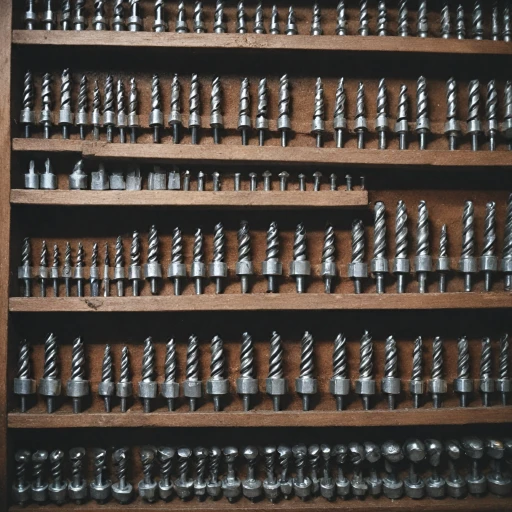
Understanding SDS Drills
A Dive into the World of SDS Drills
SDS drills have become a staple in many toolboxes, known for their powerful hammering action and efficiency. Understanding SDS drills is crucial for selecting the right model tailored to your needs. Let's explore what sets these drills apart and their unique components.
SDS, which stands for "Slotted Drive System" or "Special Direct System," refers to a specific mechanism that secures the drill bits in rotary hammers. This system ensures a strong grip, allowing the drill to efficiently perform heavy-duty tasks. These drills are typically used for high-demand applications like concrete masonry drilling, where both power and durability are required.
The SDS drill features a distinct carbide head, designed to endure tough masonry drilling. The tool's ability to accommodate various sizes, including inch SDS and larger diameter, offers flexibility for different project requirements. Notably, the length of the bit plays a pivotal role in reaching deeper areas with precision, making it a versatile tool in the rotary hammer drill category.
There are different types of SDS drills: SDS Plus, SDS Max, and SDS Bulldog. Each type supports specific drilling tasks and can work with compatible bits, such as SDS carbide, enhancing the ease of penetration in masonry and concrete. The choice of the drill often depends on the total power required and the specific bit model being used.
For those looking to add more functionality to their toolset, pairing the right SDS drill with appropriate bits can significantly impact performance. Understanding the capabilities of each type is essential when choosing the perfect tools for your needs. In subsequent sections, we'll delve deeper into choosing the right SDS drill with bits and explore various applications and comparisons between corded and cordless models.
Choosing the Right SDS Drill with Bits
Selecting the Perfect SDS Drill for Your Needs
Choosing the right SDS drill accompanied by suitable bits entails careful consideration of several factors. The primary decision lies in identifying the appropriate SDS model that aligns with your tasks, whether it involves masonry, concrete masonry, or simple rotary drilling. Here's a succinct guide to aid your decision-making:- Drill Purpose: Determine whether your work requires a hammer or rotary hammer action. For tasks involving concrete or hard materials, a rotary hammer model offers superior efficacy.
- Bit Compatibility: Ensure compatibility of the SDS bit with your drill's diameter and length specifications. It's crucial to match the inch size of the bit with the drill's chuck requirements.
- Type of Tasks: The bit's construction—such as carbide or sds carbide—is essential for the durability and effectiveness of drilling. For heavy-duty drilling, a carbide drill or sds max with carbide head enhances performance.
- Workpiece Material: For optimal results in concrete drilling, bits sds equipped with a head design specific for hammer drilling are recommended.
Applications of SDS Drills
Discovering the Practical Uses of SDS Drills
SDS drills are renowned for their versatility and their capacity to handle various tasks, making them invaluable tools in both professional and DIY projects. From concrete drilling to masonry work, let's explore the diverse applications that make SDS drills a go-to choice for various jobs. Concrete and Masonry Drilling One of the primary applications of SDS drills is their exceptional ability to tackle concrete and masonry tasks. Equipped with carbide drill bits, these tools effortlessly penetrate concrete structures, offering precision and efficiency. Whether you're working with a masonry drill to craft holes in concrete walls or using a rotary hammer to tackle tougher materials, the SDS bits ensure smooth and effective performance. Handling Various Bit Models and Sizes An SDS drill's capability expands with the use of different bit models and sizes. For instance, employing a larger diameter bit can make quick work of larger holes, while smaller bits with a diameter of inches offer precision for more delicate tasks. Coupled with varying lengths—such as inch SDS, which offers depth options—these drills cater to a wide range of drilling needs. Comprehensive Tool Packages Using an SDS drill often involves working with a complete pack of tools tailored for specific applications. Many sets come with a variety of drill bits and rotary hammer bits, catering to both general drilling and specialized masonry work. This versatility ensures that, whether the task at hand involves bits SDS or SDS carbide, the right tool is always within reach. SDS Bulldog and SDS Max Variants For more demanding projects, the SDS Bulldog and SDS Max models offer enhanced power and durability. These variants are particularly useful in professional settings, where precision and efficiency are paramount. By using a hammer drill in combination with these powerful models, users can confidently tackle even the toughest challenges in construction or renovation. Mastering the art of using these versatile tools not only enhances efficiency but also expands possibilities in various fields, from construction to home improvement projects. Understanding their potential allows for a more informed choice when selecting the right tools and bits for your specific needs, enhancing both performance and outcome.Comparing Cordless and Corded SDS Drills
Evaluating Mobility and Power in SDS Drills
The choice between cordless and corded SDS drills often boils down to factors like mobility, power needs, and the specific working environment. Both types of drills have their advantages and it's crucial to evaluate how they align with your drilling tasks.- Mobility and Convenience: Cordless SDS drills offer unparalleled mobility, making them ideal for sites where a power source isn't readily available. Their battery-powered nature means you can easily navigate tricky angles or heights without being restricted by cords. On the other hand, corded drills are bound by the length of the power cable, which can be impractical in some scenarios.
- Power and Performance: Corded SDS drills are typically known for their uninterrupted power supply. This makes them a preferred choice for heavy-duty tasks such as drilling into hard concrete masonry. The continuous power ensures that hammering and rotary actions remain consistent, especially when using bits with a larger diameter or longer length inch.
- Applications and Suitability: For tasks that demand high power output, like using drill bits with an inch SDS or SDS max for concrete masonry, a corded model could be beneficial. On the flip side, for jobs requiring maneuverability and ease of movement, a cordless model equipped with carbide drill bits might be more suitable.
- Drilling Tasks and Tools: When comparing the two, it’s also worth considering the related tools and accessories. Cordless SDS drills typically come with additional battery packs, ensuring you have a backup when one runs out. This is crucial for extended projects that require sustained hammer drilling.
- Weight and Ergonomics: Many professionals consider the weight of the tool. Corded models tend to be slightly heavier due to their robust motors, whereas cordless models can be bulky depending on the battery but are generally lighter. This difference can impact user fatigue over longer periods of use.
Maintenance Tips for Your SDS Drill Set
Keep Your SDS Drill Running Smoothly
Maintaining your SDS drill set is essential for prolonging its life and ensuring optimal performance. A well-maintained drill saves you time and money in the long run, especially when working with challenging materials like concrete and masonry.
Routine Cleaning and Inspection
Start with regular cleaning of your tools. After each use, wipe down your SDS drill, bits, and accessories, removing any dust or debris. For areas around the head and chuck, ensure no foreign particles are causing blockages. Check all screws and connections for tightness and look for any loose or worn-out parts that may need replacement.
Proper Lubrication Practices
Lubrication is key to keep your SDS drill functioning efficiently. Apply a few drops of oil to the chuck and moving parts periodically. This practice helps in reducing friction, enhancing the longevity of your tools. While doing so, confirm that your drill bits – especially those with carbide tips – are sharp and in good condition. A blunt bit can cause undue stress on both the drill and the user.
Inspecting Drill Bits
Examine your drill bits regularly, particularly those with carbide tips that tend to wear out faster during heavy drilling. Check for signs of wear or damage on bits of varying length, diameter, and inch formations. Replacing worn bits helps maintain efficiency when tackling materials like concrete and masonry.
Battery Care
If using a cordless model, take special care of your battery. Avoid complete discharge and store your batteries in a cool, dry place to optimize their life. Consistent charging only when necessary can lead to better performance over time.
In Summary
By incorporating these maintenance tips into your routine, you can ensure that your SDS drill set remains a reliable and efficient part of your toolkit for years to come, whether you are using it for heavy-duty hammer drilling or precise rotary tasks on concrete and masonry surfaces.
Safety Precautions When Using SDS Drills
Ensuring a Safe Drilling Experience
Safety should remain a top priority when working with SDS drills. These powerful tools, especially the SDS rotary hammers, can handle concrete and masonry effectively, but they also demand respect and caution.- Wear Protective Gear: Always equip yourself with safety goggles, gloves, and ear protection. The noise from the rotary hammer drilling into concrete can be intense, and shards of material can become airborne.
- Check Tools Regularly: Before starting, inspect your drill, carbide bits, and any attachments. Ensure the SDS bits are securely fastened and the drill head is in good condition. Loose bits can easily lead to accidents.
- Correct Tool Usage: Understand your drill model's capabilities. Some models, like SDS max, handle larger diameter bits, sometimes up to an inch in diameter. Utilizing a bit that's not suited for your drill can cause it to malfunction or damage materials.
- Stable Work Environment: Ensure that your work area is stable and clear of obstructions. A firm grip on your drill and a stable stance will prevent accidents caused by sudden movements or drill kickbacks.
- Follow Manufacturer Guidelines: Manufacturers provide detailed instructions for SDS drills. Adhering to these guidelines, such as the specified length for bits or the total pack weight your tool can handle, will help maintain safety and performance.
- Be Aware of Surroundings: Be cautious of the environment when drilling into concrete or masonry. Consider the presence of electrical wiring, plumbing, or conduits. Prior knowledge of what's behind the surface can prevent costly and dangerous mistakes.